A Heat Exchanger like no other?
- Gaurav
- Jun 25, 2020
- 2 min read
Updated: Dec 14, 2020
GE Research has claimed to have designed 'a heat exchanger like no other'. In this project, using an image in the public domain and my imagination, I recreated the model in SOLIDWORKS and compared its performance with a traditional heat exchanger using COMSOL.

Additive manufacturing, with its design freedom, has enabled us to revisit traditional designs not only in structural but also in thermo-fluid applications. In this respect, GE Research has claimed to have designed 'a heat exchanger like no other'.
“So exactly how better is this heat exchanger? I try to answer the question in this project.”
Scope of the project
From the available image in the public domain, recreate the model in SOLIDWORKS using my imagination.
Estimate its performance using COMSOL.
Benchmark against a traditional heat exchanger with the same: total occupied volume, weight and mass flow rates.
Solid modeling

The main challenge in solid modeling the heat exchanger was the limited resource. Just one image was available in the public domain. The challenge of recreating the complicated geometry using my own imagination got me excited. From the image alongside, I seem to have succeeded in recreating the complex geometry.
The SOLIDWORKS features used were Revolve, Revolve-cut, Mirror, Circular Pattern, Assembly, etc.
What exactly is the novel design?
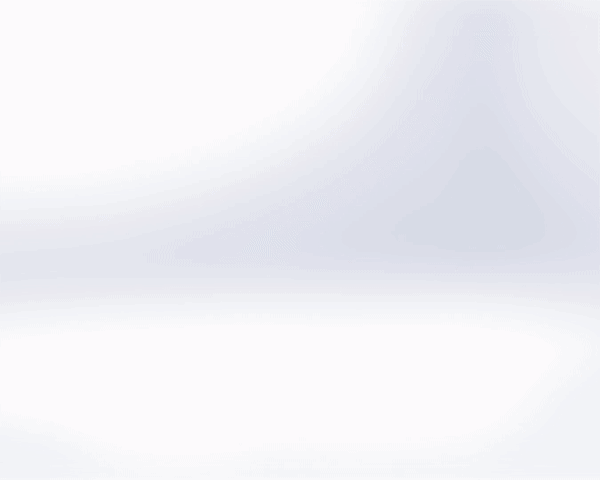
As can be seen above, the red flow path is tubular and 'trifurcating' while the blue is highly complex with no standard geometric features. The red flow path splits and recombines repeatedly. The blue encounters this maze of trifurcating tubes.
The animation alongside can better help visualize the complex flow paths.
How does it perform?
Assumptions:

Symmetry exploited to reduce the computational cost (One-third of the domain is solved for with symmetry bcs)
Steady state
Laminar flow
Counter-flow arrangement
Working fluid is water on both sides
Result:
Thus, a temperature rise of 20 degC could be obtained at a cost of 0.747 Pa pressure drop.
Bench-marking against a traditional heat exchanger

For a fair comparison, the following quantities are kept a constant:
Total occupied volume
Weight
Mass flow rates & inlet conditions
The traditional heat exchanger has simple rectangular flow paths. The hot and cold fluids flow in alternate rows. The relatively simple geometry makes them manufacturable by traditional methods.
How does the traditional HEx perform?
Assumptions:
Again, Symmetry exploited (Half of the domain is solved for with symmetry bc)
Steady state, Laminar flow, Counter-flow arrangement
Working fluid is water on both sides
Assumed data is the same as for GE HEx
Results:
Thus, a temperature rise of 6 degC could be obtained at a cost of 0.031 Pa pressure drop.
Conclusion
For the following quantities kept constant:
Total occupied volume
Weight
Mass flow rates & inlet conditions
As compared to a traditional HEx, the GE HEx has 3.33 times more heat transfer with 24 times more pressure drop
Comments